Samarium Cobalt Disc Magnets SmCoDiscover our range of samarium cobalt (SmCo) disc magnets, a strong permanent magnet often used in automotive and industrial manufacturing applications. Samarium cobalt is what’s known as a rare-earth magnet, which is a permanent magnet made from alloys of rare-earth elements – in this case, samarium. These types of magnets only lose minute amounts of magnetism over time, making them essential in a huge range of industries. Samarium Cobalt Disc Magnets are used in the Design & Manufacturing of Weather Station Equipment. Also valve monitoring equipment, precision and concept to design engineering. High temperature resistance. |
Samarium Cobalt (SmCo) Disc magnets
Samarium cobalt (SmCo) is a type of rare earth magnet that has the ability to operate in high temperatures and has superior resistance to corrosion. Similarly to many other rare earth magnets samarium cobalt is brittle and can be chipped and cracked easily making them unsuitable for applications that require repetitive direct impact to the surface of the magnet. These magnets are often best used in applications where the magnet is recessed into a hole or groove to protect the magnet from impact. This high performance, high temperature magnet is typically found in food and industrial manufacturing industries. SmCo is the alternative to Neodymium magnets when a more stable output over a much wider temperature range is required. The SmCo magnets can be used from temperatures nearly as low as absolute zero (-273°C) up to +350°C. Although Neodymium magnets provide stronger fields at room temperature, SmCo starts to outperform at temperatures above +150°C. With superior temperature coefficients than Neodymium, magnetic output from SmCo varies less over a change in temperature, making it an ideal choice for temperature sensitive applications such as sensors and loudspeakers where stability of the field during operation is important. SmCo also has a very good intrinsic coercivity allowing it to be used in applications where high external demagnetising forces (and high temperatures) may be present, such as the starting of an electric motor. SmCo has very little free iron in its structure meaning it offers excellent corrosion resistance to water. It very rarely requires protective coating (e.g. a nickel coating to allow soldering to a printed circuit board). Because of its performance characteristics SmCo is often used instead of Neodymium in mission critical applications such as aerospace and military applications.
SMCO DISC MAGNETS
Samarium cobalt (SmCo) disc magnets are made of an alloy of samarium and cobalt. They have strong magnetic strength like as neodymium disc magnets.The reason why SmCo disc magnets are widely used is their ability to maintain magnetic force. For example, SmCo disc magnets can work in applications that operate at extremely high or low temperatures.
If you need rare earth disc magnets that are not easily corroded or oxidized, then samarium-cobalt (SmCo) magnets will be available. Protective coating is usaually not needed for SmCo disc magnets. However, we recommend that you use them with care because they are fragile and easy to crack or chip.
PURCHASE NOW AT MAGNOSPHERE - SmCo Disc Magnets, buy strong rare earth (Neo or NdFeb) Magnets!
SmCo Magnets / Samarium-Cobalt (SmCo) Rare Earth Magnets
Samarium Cobalt rare earth magnets are often used in high temperature applications needing high magnetic performance and where magnetic stability over a wide range of temperatures is important. Magnosphere can help optimize performance and cost with SmCo magnets in grades from 16 to 32 MGOe and temperatures up to 350°C/662°F. Stock Samarium Cobalt magnets also available to reduce development and production lead times.
Available Grades of Samarium Cobalt Magnets:
Many grades of Samarium Cobalt exist to support a variety of industrial and commercial applications. The range of Samarium Cobalt Magnet grades is typically 16 to 32 MGOe. These ranges allow for balancing cost, magnetic performance, and operational temperature resistance.
Many grades of Samarium Cobalt magnets exist to support a variety of industrial applications. The range of SmCo magnet grades typically extends from 16 MGOe to 32 MGOe. This range allows for optimizing cost, performance, and operational temperature resistance.
There are two main types of Samarium Cobalt magnet alloy. The older version, typically denoted as (1-5) having one Samarium atom per 5 Cobalt atoms, and the newer Samarium Cobalt magnet alloy, typically denoted as (2-17), having an atomic ratio of two Samarium atoms to 14 – 17 Cobalt atoms. (The 14 – 17 atoms are actually comprised of a mix of transition metals, Cobalt, Copper, and Iron, where Cobalt is the most abundant.)
Corrosion Resistance:
SmCo Rare Earth magnets are very resistant to corrosion and do not normally require any surface treatment.
Samarium Cobalt magnets exhibit good corrosion resistance when compared to Neo magnets. For most applications a coating or plating is not required, but it should be considered when operating in environments that are acidic, have high moisture, or are in a vacuum.
Coatings and metal platings can be applied to increase the ability to clean the magnet. A metal plating will allow for greater cleanliness for vacuum and medical applications. Nickel plating can be applied to facilitate soldering the magnet, and this is especially used for adhesion to a printed circuit board.
Low environmental reactivity makes Samarium Cobalt magnets good candidates for Medical and Aerospace applications. It is always advisable to empirically evaluate the magnet alloy in the operational environment before deciding on a design path. Typically, Samarium Cobalt magnets used in Medical applications will be parylene coating in addition to being clad in an application appropriate material.
Temperature Effects:
Samarium Cobalt Magnets can operate at temperatures up to 500F (260C), making these rare earth magnets ideal for high heat applications.
Sintered Samarium Cobalt rare earth magnets are extremely resistant to demagnetization and can operate at temperatures up to 500F (260C). There are many Samarium Cobalt grades which can withstand higher temperatures, but several factors will dictate the overall performance of the Samarium Cobalt rare earth magnet. One of the most pertinent variables is the geometry of the magnet or magnetic circuit. Samarium Cobalt magnets, which are relatively thin compared to their pole cross-section (Magnetic Length / Pole Area), will demagnetize easier than Samarium Cobalt magnets which are thick. Magnetic geometries utilizing backing plates, yokes, or return path structures will respond better to increased temperatures. The maximum recommended operating temperatures listed on the Samarium Cobalt magnetic characteristics page do not take into account all geometry conditions. Please contact a Magnosphere team member for Samarium Cobalt rare earth magnet design assistance when elevated temperatures are involved in your application.
Magnetization Options:
Although most commercial magnets are anistropic, which means they have a preferred direction of magnetization, various pole configurations can be achieved without conflicting with a Samarium Cobalt Magnet’s orientation.
Most useful commercial magnets are anisotropic which means that they have an “Easy” or preferred direction of magnetization and that an orientation field was applied during the compaction stage of the manufacturing process.
It is essentially impossible to magnetize the resulting anisotropic magnet alloy other than in the Direction of Orientation; however, various pole configurations can be achieved without conflicting with the magnet material’s orientation.
Compliance and Intellectual Property Considerations:
Samarium Cobalt magnets manufactured by Magnosphere are compliant with Intellectual Property Rights, Environmental Restrictions, and Conflict Mineral usage.
- DFARS Compliant
- RoHS, RoHS II and REACH
- Dodd Frank Wall Street Reform Act (Section 1502)
Magnosphere stocks the most relevant magnet alloys which are applicable to DFARS. Magnosphere can design, fabricate, and provide finished magnets compliant with DFARS. The relevant magnet alloys are generally Alnico and Samarium Cobalt (SmCo).
The DFARS clauses listed above specify what is considered a “Specialty Metal” and how it can legally be procured and supplied for pertinent government contracts. More specifically to Department of Defense (DOD) article acquisitions.
The clauses also describe what is considered a “Specialty Metal” and how it may be incorporated into a down- stream product. Several magnetic alloys fall under the classification of a “Specialty Metal.” The most commercially relevant are Samarium Cobalt (SmCo) and Aluminum Nickel Cobalt (AlNiCo), but lesser used alloys can also fall under the Specialty Metals clauses. The best way to mitigate risk is to ascertain if the magnet alloy contains Nickel or Cobalt and determine if the concentrations of these metals are sufficient to classify the magnet alloy as a Specialty Metal.
Handling and Storage of Samarium Cobalt Magnets:
SmCo Magnets are very strong and brittle, requiring appropriate handling and packing to ensure safety and prevent damage.
Samarium Cobalt Magnets are very strong and brittle, and appropriate handling and packing is required. Most receiving departments are not familiar with the strength of Samarium Cobalt magnets and this can result in injury or broken parts. All personnel that may come in contact with this alloy should be made aware of the dangers of handling these magnets. The brittle nature of the alloy can lead to flying chips if the magnets are allowed to impact each other or a solid surface. Larger magnets can become a pinching hazard if caution is not exercised. We urge all customers to discuss handling techniques pertinent to their magnets with a Magnosphere team member.
Samarium Cobalt Magnet Manufacturing Methods:
Samarium Cobalt Magnets are typically manufactured by a powdered metallurgical process utilizing rigid steel or rubber molds.
Fully dense Samarium Cobalt rare earth magnets are usually manufactured by a powdered metallurgical process. Micron size Samarium Cobalt powder is produced and then compacted in a rigid steel mold. The steel molds produce shapes similar to the final product, but the mechanical properties of the alloy usually inhibit complex features at this stage of the manufacturing process.
The Samarium Cobalt’s magnetic performance is optimized by applying a magnetic field during the pressing operation. This applied field imparts a preferred direction of magnetization, or orientation, to the Samarium Cobalt magnet alloy. The alignment of particles results in an anisotropic alloy and vastly improves the residual induction (Br) and other magnetic characteristics of the finished magnet.
After pressing, the Samarium Cobalt magnets are sintered and heat treated until they reach their fully dense condition. The rare earth magnet alloy is then machined to the final dimensional requirements and cleaned.
Process of Making Rare Earth Magnets
- The rare earth magnets are made by using different process involving various stages. The popular stages of the production of rare earth magnets are:
- The first stage is the manufacture of rare earth element alloys.
- The metal alloy is then finely powdered.
- The next step involved is pressing of powder either isostatically or pressing through die process.
- The particles so pressed are oriented.
- Sintering of the element is done accordingly.
- The shapes are then sliced into desired shapes and sizes.
- The coating is done thereafter.
Purchase Now: Neodymium Magnets online
![]()
|
![]()
|
![]()
|
![]()
|
![]()
|
![]()
|
![]()
|
![]()
|
![]()
|
![]()
|
![]()
|
![]()
|
We ship our Magnets worldwid via Sea or Air Shipment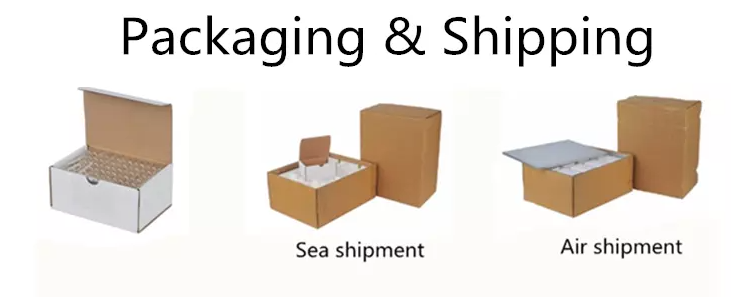
Who supplies high quality Samarium Cobalt Disc Magnets?
Magnosphere produces magnets at great prices, produced and delivered on time for all areas of industry, automotive, aerospace, electronics as well as in the design sector, trade fair construction, offices and for the home.
We are an ISO certified shop and carry the Trusted Shops seal. We have successfully completed more than 300,000 orders and offer our ever-growing customer base 24/7 customer service.
All items are available for immediate delivery in large numbers with daily dispatch. Our selection is your win! Thousands of satisfied customers! Buy from a company with the highest quality standards and customer service with flexible and diverse payment options and conditions.
We can also custom manufacture these to fit your exact specifications using our in-house global manufacturing facilities and team of experienced engineers. Need high quantities of magnets at the lowest and fairest price possible? Just let us know what you are looking for and contact our Customer Care Team by sending us a request for quote! We'll work with you to determine the most economical way of providing you with what you need.
Trust in our experience and convince yourself of our service and our products and we look forward to welcoming you to our magnet shop at Magnosphere. You are welcome to contact us by eMail: info(at)magnosphere.co.uk. Available 24/7 x 365 and we are also there for you on public holidays! Or just give us a call.
ROHS-Directive
Magnosphere conforms to the RoHs directive and the Reach and PFOS regulations. Directive 2002/96 / EC of the European Parliament and of the Council, of January 27, 2003, on waste electrical and electronic equipment (WEEE).

- Hotline:+49 (0) 2241 959450
- Telefax: +49.2241.9594520
- eMail: info@magnosphere.co.uk
We are very proud to offer excellent customer service. We know that without our clients, we would not be here. If you have any questions about your order or something else, please call or email us!: info(at)magnosphere.co.uk
24 / 7 x 365 Including holiday periods! Our customer service team is available to help you!